
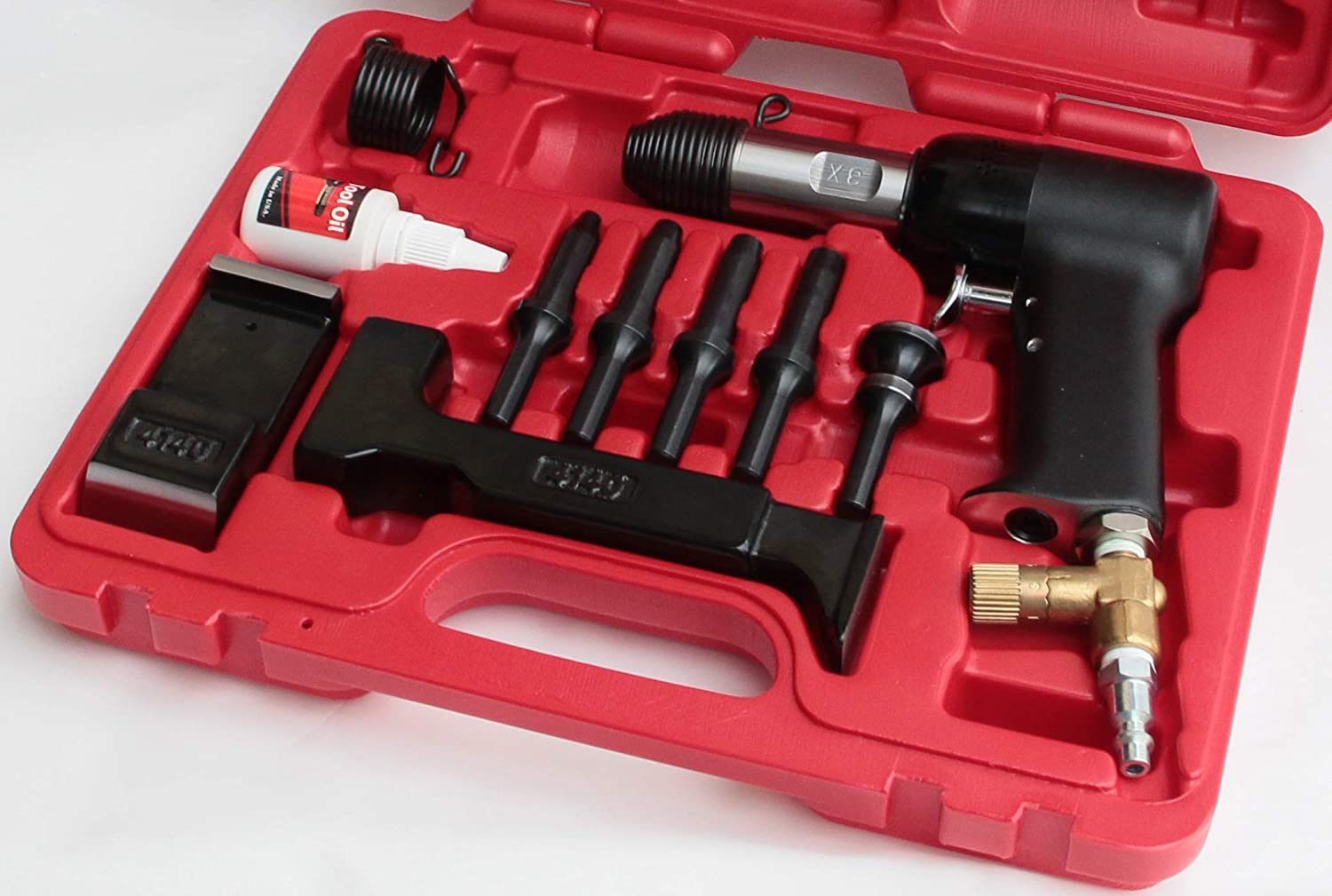
In addition, you should acquire a couple of 12" long (#30 and #40) drill bits for drilling in hard to reach places.īecause these long bits can be easily flexed with your fingers they can be made to drill close to corners, and just about anywhere else that a 90 degree angle drill would otherwise have to be used.
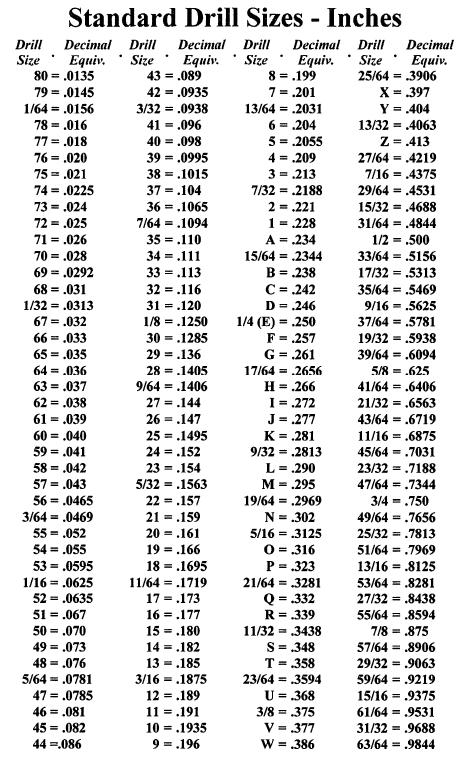
However, the tougher, more expensive, Cobalt bits should be used to drill hardened steel parts like landing gear legs and engine mounts. The type of drill bit you will probably use the most is the High Speed Drill (jobbers length) because of its ready availability and low initial cost. Read on to see how you can avoid or at least limit your encounters with these, all too common, hole preparation problems.
#BUCK RIVET DRILL BIT SKIN#
Forgetting to dimple the top and/or bottom skin for flush riveting.Forgetting to deburr the holes in both skins.However, as if all that isn’t bad enough - after the hole is drilled you can still create other problems by: Drilled O.K., but only after scratching the skin.After all, with thousands of holes to be drilled in a typical all-metal aircraft project, the "opportunity" exists for some of those holes to be:
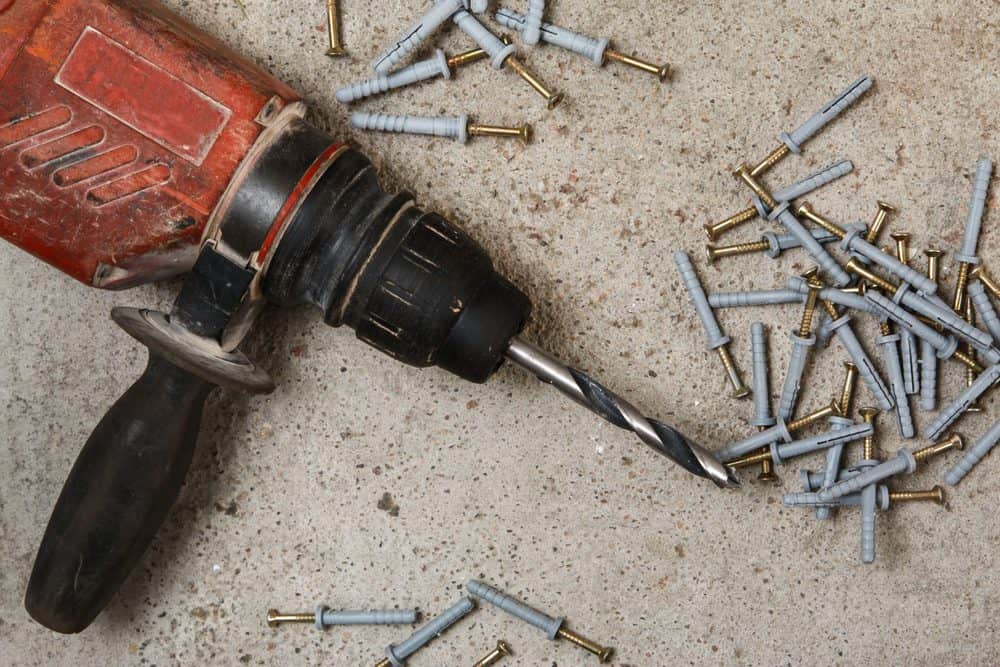
However, not everyone can drill a nice round hole - in thin metal - where it needs to be - and do it right every time. Repairs to more than two adjacent oversize rivets, or replacing more than half the rivets with oversize rivets in any 10 inch length of pattern is prohibited.It’s true, anyone can drill a hole.

Repair limitations: The combined oversize rivet hole repairs and oversize countersink repairs should be limited to a maximum of 20 percent of the rivets, or 10 rivets in a single rivet pattern, whichever is less. The term "next larger size" shall be defined as the next larger diameter for the application, but not to exceed 1/32 inch increments for sizes up to 1/4 inch diameter and 1/16 inch increments for sizes above 1/4 inch. Oversize countersinks: When countersinks are enlarged beyond specified tolerances, the next larger size rivet may be used, provided pitch and edge margin design requirements are maintained. Burrs may be removed from rivet holes by chamfering to a depth not to exceed 10 percent of the stock thickness, or 0.032 inch, whichever is less. Mating surfaces should be cleaned before parts are riveted together, all chips, burrs and foreign material must be removed from the mating surfaces. If piercing is used, all holes need be inspected for radial cracking. Piercing Only piercing tools which produce-true and clean holes, equivalent to acceptable drilled holes should be used. When drilling through more than one sheet, hold the sheets securely together so there is no misalignment of holes due to shifting or separation of the sheets. Extreme pressure shall not be applied and holes shall not be punched through with the drill.Ĭ. All holes shall be drilled normal (at 90 degrees) to the working surface.ī. Drilling Rivet holes should be drilled in accordance with the following recommendationsĪ.
